3.2.1.4.4硫化溫度、時間與壓力的影響
硅橡膠的熱硫化作用通常由兩個階段組成:加壓或不加壓的預硫化和在熱空氣中的無壓后硫化。最新的膠料配合往往可以省去后硫化。上述大多數有機過氧化物能用于加壓預硫化。但是,實際上最常使用的是叔丁基異丙苯基過氧化物和二異丙苯基過氧化物,因為它們的分解溫度比較高。與分解溫度較低的二芳酰基過氧化物相比,這兩種物質在溫度未達到大約136°C之前是不會活化的,因此,它們一般需要在150~170°C的溫度下進行硫化。
上述一些有機過氧化物如不加壓進行預硫化,就會起泡。與此不同,雙-2,5-二氯二苯甲酰過氧化物則可在熱空氣中進行無壓預硫化而不起泡。為了避免變形,在無模硫化時可以用比平板硫化時所需要的溫度更高一些。但在平板硫化時定要使膠料能夠流動。用二芳酰基過氧化物時,為了避免焦燒,平板硫化溫度最好不超過110°C太多。但是若在熱空氣中進行無模硫化時,由于硅橡膠有極好的高溫穩(wěn)定性,可用200~300°C的溫度硫化。在這樣高的溫度下,預硫化是如此之快,以致可以在熱空氣管道中或在加熱運輸帶上進行硫化。
不管預硫化是否在加壓情況下進行,后硫化總是需要的。
硅橡膠制品進行后硫化處理的主要原因有二:首先可以除去過氧化物在硫化時分解產生的揮發(fā)組分;其次能使物理和化學性能達到最宜水平。為了除去分解產物,后硫化溫度和時間必須超過一定的最低值。過氧化物的所有分解產物通常都可以在200°C左右的溫度范圍內后硫化1~3小時之后除去,但是這樣做一般不能保證有最好的物理或化學性能。因此,實際上在200°C左右范圍內的溫度要保持12~18小時。一般地說,后硫化的溫度和時間取決于硫化膠的使用要求和過氧化物分解產物的揮發(fā)性。
過氧化物引起的預硫化交聯(lián),可以被(大氣中的)氧所干擾。但是后硫化過程中,過氧化物在實際上已不再存在,再增加的交聯(lián)作用是由于氧的作用引起的。所以,在后硫化進行中,一定的最低氧量總是需要的。如果含氧低于這種最低值,后硫化便將不合理想,而硫化膠達不到應有的性能,其中硬度不夠高,有時甚至能使硅橡膠解聚而報廢。
高于180°C的老化過程主要受兩個相反的過程所控制;水解解聚作用和有機側基基團的裂解。高分子鏈狀二有機聚硅氧烷,亦即硅橡膠的水解解聚結果,形成類似硅油的低分子物質(見方程式228a)。隨后硫化膠變軟,實際上表現為邵氏硬度和彈性下降。

如果硅橡膠制品的穩(wěn)定性完全取決于水解解聚,那末制品應該在使用過程中慢慢變軟。
第二個過程是在高于100°C情況下,由于大氣氧的作用使有機側基基團分裂出去,結果產生交聯(lián)而使硫化膠變硬(見方程式228b)。實驗表明,即使在溫度很高的情況下,解聚作用也僅在老化開始時占優(yōu)勢。
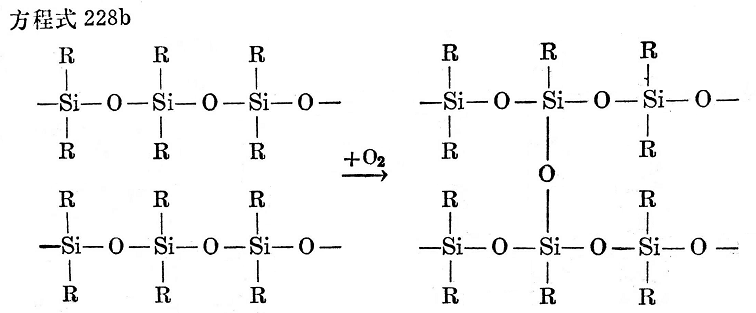
熱氧化交聯(lián)是用催化劑諸如鐵、鈦、鈰、鑭等化合物或類似物質而加速的。在180°C以上的溫度下充分老化時,交聯(lián)最后占優(yōu)勢,硫化膠變軟并于彈性降低之后便逐漸變硬。交聯(lián)一直繼續(xù)到所有的有機基團裂解而硅橡膠變成硅酸為止。
硅橡膠的抗氧交聯(lián)作用比抗水解解聚大得多,因此,當氧氣不足時,它特別容易早期老化。換句話說,沒有氧,硅橡膠便不是特別耐高溫的。這意味著硅橡膠與有機彈性體不同,用于170~180°C以上的高溫時,必須暴露在空氣中,否則將喪失其著名的穩(wěn)定性。因此,在進行后硫化時,硅橡膠應該與足夠的氧氣接觸,為此,每公斤硫化膠每分鐘需要120~125公升的空氣。
已經講過,有機過氧化物的結構能大大影響硫化膠的性能。為了仔細研究這種影響,測定了由含有噴霧二氧化硅加0.6重量份活性過氧化物的硅橡膠之硫化膠的各種機械性能,從而發(fā)現過氧化物的選擇決不是無關緊要的。一向被稱為“經典過氧化物”的二異丙苯基、叔丁基異丙苯基、和二叔丁基等過氧化物能使硅橡膠具有良好的全面性能。過氧化二苯甲酰雖以產生高定伸強力著名,但抗張強度較低。用過苯甲酸叔丁酯所得膠料也有高的定伸強度,而用過辛酸叔丁酯的硫化膠的定伸強度則很低。象比較老的產品2,5-二甲基-2,5-雙(叔丁基過氧)己烷一樣,一些新出現的過氧化物,例如2,5二甲基-2,5-二(叔丁基過氧)己炔-3和1,4-雙(叔丁基過氧異丙基)苯等,也給予硫化膠非常好的性能。但是,用2,5-二甲基一己基-2,5-二過氧苯甲酸酯所生產的制品,在后硫化后機械性能大為降低。
硅橡膠交聯(lián)的主要方法,將在3.11.1、3.11.2和3.12.3中敘述。